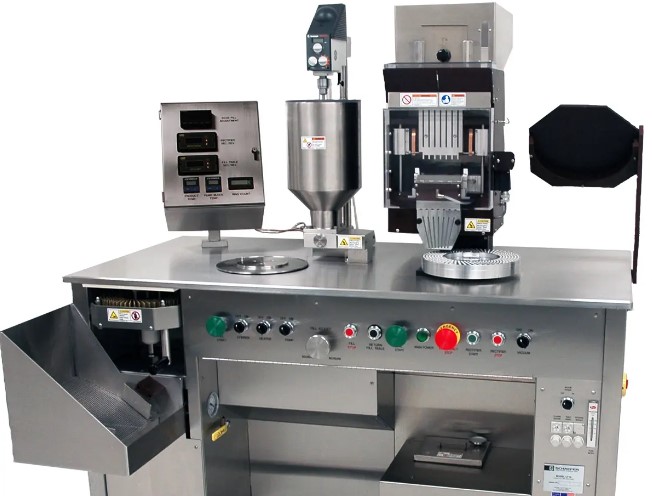
A Guide to Capsule Filling Equipment for Pharmaceutical Companies
When it comes to pharmaceutical companies, efficiency and accuracy are of utmost importance. This is why investing in the right capsule filling equipment is crucial for ensuring the quality and effectiveness of medications. In this guide, we will explore the ins and outs of capsule filling equipment for pharmaceutical companies, from understanding the technology to overcoming common challenges and looking towards the future.
Understanding Capsule Filling Equipment
Capsule filling equipment plays a pivotal role in the pharmaceutical industry, providing an essential means for accurately dosing and encapsulating a wide range of medications. These machines come in various formats, including manual, semi-automatic, and fully automatic models, designed to cater to different production needs and scales. Manual capsule fillers are often suited for smaller operations or special applications where precision and flexibility are paramount, but production volumes are lower. Semi-automatic machines offer a balance, increasing output while still requiring some manual oversight. Fully automatic capsule fillers, on the other hand, represent the pinnacle of efficiency and consistency, capable of processing thousands of capsules per hour with minimal human intervention.
Each type of machine has its unique mechanism of operation, but the core process typically involves separating the capsule halves, filling them with a specified quantity of product—be it powder, granule, or liquid—and then rejoining the halves before ejecting the completed capsules. The choice between these machines depends largely on the specific requirements of a pharmaceutical company, including production volume, desired level of automation, and the physical characteristics of the medication being encapsulated.
Furthermore, the technology embedded in these machines has evolved significantly over the years, introducing sophisticated features such as vacuum positioning for capsule separation, precision dosing tools for accurate fill weights, and advanced control systems to monitor and adjust the operation in real time. These advancements have not only enhanced the reliability and efficiency of capsule filling processes but have also contributed to higher standards of medication safety and efficacy by ensuring consistent dosage strengths.
Choosing the right capsule filling equipment is a critical decision for pharmaceutical manufacturers, as it directly impacts the quality of the final product and the efficiency of the production line. With a clear understanding of the types of machines available and their operational capabilities, companies can make informed investments that align with their production goals and quality standards.
The Advantages of Modern Capsule Filling Technology
In today’s fast-paced pharmaceutical manufacturing environment, leveraging modern capsule filling technology presents a host of advantages that go beyond mere productivity gains. One of the most significant benefits is the enhanced precision it brings to dosing. With state-of-the-art equipment, the margin for error in filling capsules with the exact dose of medication is drastically reduced. This precision ensures that each capsule contains a uniform amount of the active ingredient, which is critical for patient safety and therapeutic efficacy.
Another key advantage is the reduction in operational waste. Advanced capsule filling machines are designed to handle materials more efficiently, minimizing the loss of valuable pharmaceutical compounds during the filling process. This not only has a positive impact on the environment by reducing waste but also contributes to cost savings for pharmaceutical companies, making the production process more economical.
Furthermore, modern capsule filling machines are equipped with features that allow for rapid production adjustments. This flexibility is essential in an industry where demand can fluctuate, and product lines may need to change in response to market needs. The ability to quickly switch between different capsule sizes or fill materials without extensive downtime for reconfiguration helps manufacturers stay responsive and competitive.
The integration of advanced control systems in modern capsule filling equipment is another notable advantage. These systems provide real-time monitoring and adjustments to the filling process, ensuring consistent quality across batches. Additionally, they can flag potential issues before they become significant problems, facilitating proactive maintenance and reducing the likelihood of costly downtime.
Overall, the adoption of modern capsule filling technology equips pharmaceutical companies with the tools they need to meet the demands of contemporary medicine production. By offering increased accuracy, reduced waste, operational flexibility, and enhanced control, these advanced machines play a crucial role in streamlining production processes and elevating the standard of pharmaceutical manufacturing.
Key Features to Look for in Capsule Filling Equipment
When selecting capsule filling equipment for a pharmaceutical operation, several critical aspects must be carefully assessed to ensure the machine aligns with both current and future needs. Capacity and speed are paramount, with the chosen equipment needing to match or exceed the company’s production targets without compromising the integrity of the capsules or the accuracy of the fills. The precision of dosing is another non-negotiable feature, as it directly influences the efficacy and safety of the final pharmaceutical product.
Ease of operation and maintenance are also crucial considerations. Equipment that is user-friendly and straightforward to clean and maintain can significantly reduce downtime and operational costs, directly impacting overall productivity and profitability. Additionally, the ability to adapt to various capsule sizes and fill materials is an invaluable feature, providing the flexibility needed to accommodate a wide range of product formulations and market demands.
Moreover, integration capabilities should not be overlooked. In an era where technology drives efficiency, capsule filling machines that can seamlessly connect with other production line equipment and software systems offer a competitive edge by enabling more streamlined operations and better data management.
Finally, it’s essential to consider the reliability of the equipment and the support services provided by the manufacturer. High-quality construction, backed by responsive, expert technical support, ensures that any issues can be quickly resolved, minimizing any potential impact on production schedules.
In essence, the decision on capsule filling equipment should be informed by a comprehensive evaluation of these key features, to ensure the chosen solution not only meets the immediate needs of the pharmaceutical company but also offers the scalability and flexibility to adapt to future challenges and opportunities.
Overcoming Common Challenges with Capsule Filling Equipment
Navigating the hurdles associated with capsule filling equipment is a critical aspect of maintaining a high-efficiency production line for pharmaceutical companies. Among the most prevalent challenges are the intricacies involved in machine calibration, the adaptability required for handling various formulations, and the imperative need for regular maintenance to ensure optimal performance.
Effective management of these issues begins with comprehensive operator training. Well-informed and skilled operators are more adept at recognizing and rectifying minor issues before they escalate into significant problems, thus maintaining continuous production flow. Ensuring that staff are up-to-date with the latest operational techniques and understanding the nuances of the equipment can dramatically reduce downtime and improve productivity.
Regular and meticulous calibration of capsule filling machines is crucial. This practice helps in maintaining the precision required for dosing, directly impacting the quality of the final product. A properly calibrated machine ensures that each capsule is filled with the exact quantity of medication, adhering to strict regulatory standards and ensuring patient safety.
Addressing formulation changes effectively is another area that requires attention. As pharmaceutical companies expand their product lines or make adjustments to existing medications, capsule filling equipment must be versatile enough to accommodate these variations without compromising on quality or efficiency. This might involve adjusting machine settings or even swapping out components to handle different materials or capsule sizes.
Finally, a proactive approach to maintenance cannot be overstated. Regularly scheduled checks and servicing of the equipment not only prevent unexpected breakdowns but also extend the lifespan of the machinery. Adopting a preventative maintenance schedule ensures that the capsule filling equipment remains in optimal condition, ready to meet the production demands of the pharmaceutical company.
The Future of Capsule Filling Technology
As we look ahead, the trajectory of capsule filling technology is set to be revolutionized by the integration of cutting-edge innovations. The forefront of this transformation is marked by the advent of automation and robotics, poised to redefine operational efficiencies and precision in capsule manufacturing. The introduction of smart machines equipped with self-optimizing capabilities will be a game-changer, enabling equipment to adjust its parameters in real-time for optimal performance. These advancements promise not only to streamline production processes but also to minimize human error, thereby elevating the consistency and reliability of pharmaceutical products.
Artificial intelligence (AI) is another pivotal development, poised to significantly impact the capsule filling sector. By harnessing AI for predictive maintenance, pharmaceutical manufacturers will be able to anticipate and mitigate potential equipment failures before they disrupt production, ensuring continuous operation and reducing downtime. Furthermore, AI-driven quality control mechanisms will bolster the assurance of capsule integrity and dosage accuracy, fostering trust in pharmaceutical outputs.
The integration of digital technologies into capsule filling processes also opens avenues for enhanced connectivity and data analytics. Manufacturers will have the ability to monitor and analyze production metrics in unprecedented detail, facilitating informed decision-making and continuous improvement efforts. This digital transformation will not only optimize production efficiency but also enable more agile responses to market demands and regulatory changes.
In summary, the future landscape of capsule filling technology is marked by a convergence of automation, robotics, AI, and digital integration. These innovations will collectively drive the pharmaceutical industry towards higher standards of efficiency, precision, and adaptability, setting a new benchmark for medication production in the years to come. If you are looking for capsule filling equipment for pharmaceutical companies, check out Schaefers.
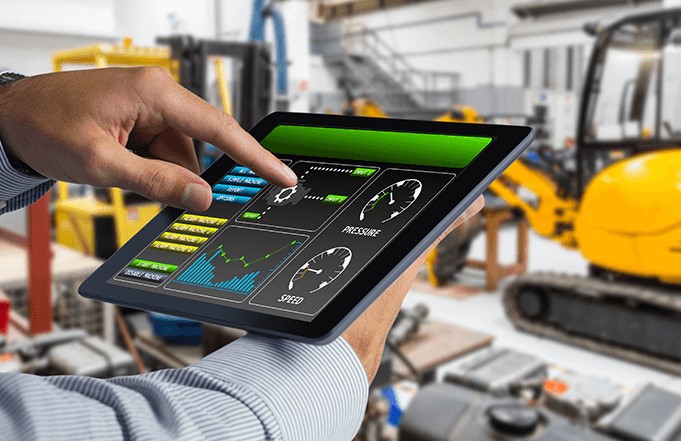
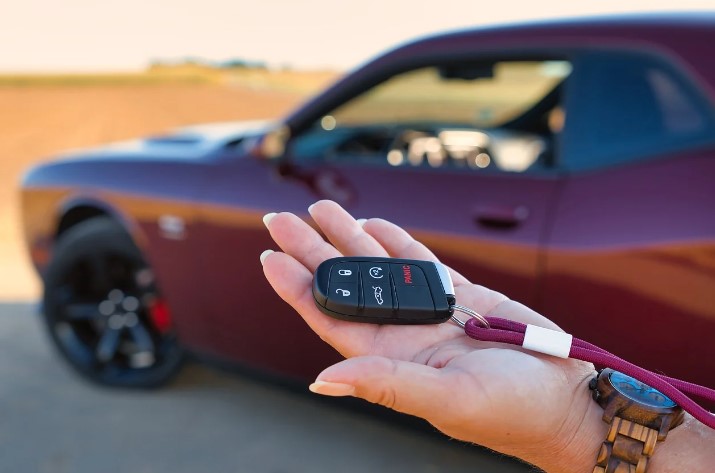