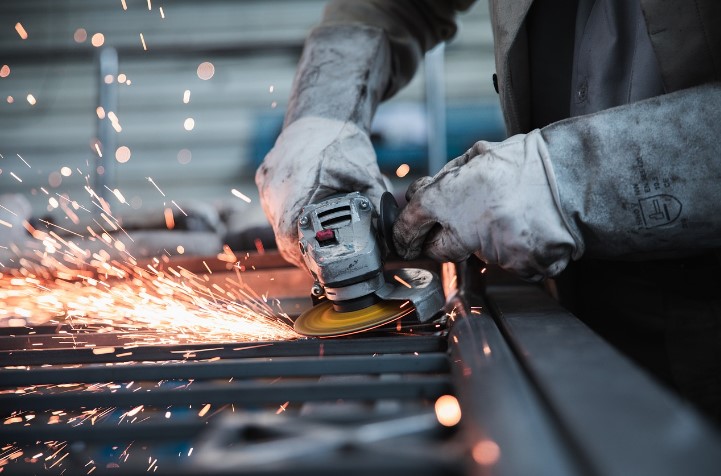
Aluminium vs. Stainless Steel: Best Metal for Fabrication?
Metal fabrication is a critical industrial process that involves the creation, shaping, and assembly of metal structures from various raw materials. As a cornerstone of sectors like construction, automotive, and aerospace, metal fabrication encompasses a wide range of techniques and practises, including cutting, bending, welding, and assembling. These methods allow for the transformation of metal sheets, rods, and tubes into precise, customised parts and products.
The choice of metal, tools, and techniques in fabrication depends significantly on the project requirements, including durability, strength, and corrosion resistance needs. With advancements in technology, metal fabrication has evolved to include highly automated and computer-controlled processes, improving precision and efficiency while reducing labour costs and errors. This makes metal fabrication a dynamic and essential field, continually adapting to meet the demands of modern engineering and manufacturing.
Importance Of Choosing the Right Metal for Specific Projects
Choosing the right metal for specific projects is paramount in achieving optimal performance, durability, and cost-efficiency in fabrication. This decision influences every aspect of a project, from design through to completion, especially when leveraging advanced 3D fabrication services.
- Material Properties: Different metals offer unique properties such as strength, weight, thermal conductivity, and corrosion resistance. For example, aluminium is valued for its lightweight nature and resistance to corrosion, which makes it particularly suitable for use in aerospace and automotive industries. while stainless steel is valued for its strength and durability, which are essential in construction and medical devices.
- Design Flexibility: The choice of metal affects the design possibilities. Advanced 3D fabrication services enable complex geometries and precise tolerances, but the suitability of a metal for these technologies is crucial. For example, metals that are highly malleable and less prone to warping under heat are preferable in intricate 3D printing applications.
- Cost-Effectiveness: Each metal carries different cost implications based on availability, ease of fabrication, and lifecycle. Initial material costs, as well as long-term maintenance and durability, need to be balanced to make a project financially viable.
- Environmental Impact: Sustainability concerns are increasingly important. Metals that are recyclable or have a lower environmental impact during production may be preferable for projects aiming for green certification or lower carbon footprints.
- Compatibility with Fabrication Techniques: Not all metals are compatible with certain fabrication techniques, including some cutting-edge 3D fabrication services. It is essential to select a metal that not only fits the technical requirements of the project but also aligns with the capabilities of the chosen fabrication technology.
Overview of Aluminium in Fabrication
Properties of Aluminium Relevant to Fabrication
Aluminium stands out in the field of fabrication due to its distinctive combination of properties that make it versatile for a broad spectrum of applications.
- Weight: Aluminum’s remarkably low weight makes it an ideal material for industries like automotive and aerospace, where minimising weight is crucial.
- Strength: When alloyed with other metals like copper, magnesium, and silicon, Aluminium’s strength is significantly enhanced, making it comparable to steel in some uses.
- Malleability: Aluminium’s malleability allows it to be easily formed into almost any shape, which is particularly advantageous in complex fabrication projects.
- Corrosion Resistance: Aluminium naturally resists corrosion and forms a protective oxide layer when it comes into contact with air, further enhancing its long-term durability.
Common Uses of Aluminium in Fabrication
Aluminium’s versatility makes it a preferred material across various industries:
- Transportation: Used in the manufacturing of frames, bodies, and components for cars, aircraft, and ships due to its light weight and strength.
- Construction: Aluminium is used in windows, doors, and structural framing for its durability and ease of maintenance.
- Packaging: Due to its non-toxicity and corrosion resistance, It is commonly utilised in the packaging of food and beverages.
- Electrical: Its excellent conductivity makes it suitable for wires, cables, and other electrical applications.
Advantages of Using Aluminium in Fabrication Projects
- Weight-to-Strength Ratio: Aluminium offers an excellent weight-to-strength ratio, which is crucial for reducing weight without compromising strength.
- Machinability: It is easy to machine and fabricate, which reduces time and costs associated with manufacturing.
- Recyclability: Aluminium is 100{53ed28d223a4415f45f82b5e3e66625b5ba2d29a1cba4099bda1615b910c8a6d} recyclable with no degradation in properties, making it environmentally friendly and cost-effective for recycling purposes.
- Thermal Conductivity: High thermal conductivity makes it ideal for applications like heat exchangers and cooking utensils.
Overview of Stainless Steel in Fabrication
Properties of Stainless Steel Relevant to Fabrication
Stainless steel is highly regarded in metal fabrication for its unique qualities that make it adaptable to a diverse array of applications:
- Corrosion Resistance: Stainless steel is highly valued for its corrosion resistance, which arises from the formation of a protective chromium oxide layer on its surface upon exposure to oxygen.
- Strength: It has a high tensile strength that can be further enhanced through various heat treatments and alloying, making it suitable for demanding environments.
- Ductility: Stainless steel is ductile and can be formed into wires, sheets, or other complex shapes without fracturing.
- Heat Resistance: Some types of stainless steel are capable of enduring high temperatures, which makes them well-suited for environments that are sensitive to heat.
Common Uses of Stainless Steel in Fabrication
Due to its robustness and aesthetic appeal, stainless steel is extensively used across numerous sectors:
- Construction and Architecture: Commonly utilised in load-bearing structures, architectural facades, and fittings because of its robustness and sleek, modern appearance.
- Medical Devices: Preferred for surgical and medical instruments because it’s easy to sterilise and has excellent corrosion resistance.
- Automotive and Aerospace: Employed in components that require durability and resistance to temperature fluctuations.
- Food Processing and Catering: Utilised in cookware, kitchen equipment, and food processing machines because it does not impart flavours and is easy to clean.
Benefits of Utilising Stainless Steel in Fabrication Projects
- Durability: One of the most durable metals available, stainless steel stands up well to impact and abrasion, which is crucial for high-use applications.
- Longevity: Its ability to resist corrosion and rust ensures that stainless steel products benefit from an extended lifespan, often outlasting those made from other materials.
- Aesthetic Quality: Stainless steel has a modern, clean look that is aesthetically pleasing and requires minimal maintenance, making it a favourite for visible architectural elements.
- Hygiene and Cleanliness: The non-porous surface of stainless steel makes it ideal for sanitary applications where hygiene is a priority, such as in hospitals and kitchens.
- Environmental Impact: Stainless steel is 100{53ed28d223a4415f45f82b5e3e66625b5ba2d29a1cba4099bda1615b910c8a6d} recyclable, and the majority of new stainless steel includes recycled material, contributing to its sustainability.
Comparison of Aluminium and Stainless Steel
Here’s a table comparing Aluminium and stainless steel across various factors relevant to fabrication projects:
Factor | Aluminium | Stainless Steel |
Cost Comparison | Generally less expensive than stainless steel, but varies based on alloy and form. Ideal for cost-sensitive applications where lightweight properties are desired. | Typically more expensive due to its alloy composition and durability. Cost-effective for applications requiring long-term durability and less maintenance. |
Durability | Highly durable in terms of corrosion resistance; however, it is softer and more prone to wear and deformation under stress unless alloyed. | Exceptionally durable with superior strength, impact resistance, and excellent corrosion resistance, appropriate for harsh environments. |
Fabrication Techniques | Easy to machine, cut, and form due to its softness and malleability. Compatible with a broad array of fabrication techniques, including welding, although it requires specific techniques due to its low melting point. | More challenging to machine and fabricate due to its hardness. Requires more advanced techniques for cutting and welding, but holds up better under high temperatures. |
Weight | Very lightweight, which reduces costs in transportation and eases installation, especially beneficial in automotive and aerospace applications. | Heavier than Aluminium, which may increase transportation costs and complicate installation but adds to structural stability where weight is beneficial. |
Maintenance Needs | Low maintenance due to its corrosion resistance; periodic cleaning is often sufficient. Anodising can enhance durability and appearance. | Requires minimal maintenance due to its corrosion resistance. Optimal for environments where high standards of hygiene and cleanliness are essential, such as in food processing and healthcare settings. |
Environmental Considerations | Highly sustainable, as Aluminium is 100{53ed28d223a4415f45f82b5e3e66625b5ba2d29a1cba4099bda1615b910c8a6d} recyclable with no loss in quality. Widely recycled and uses less energy in recycling compared to primary production. | Also 100{53ed28d223a4415f45f82b5e3e66625b5ba2d29a1cba4099bda1615b910c8a6d} recyclable and commonly recycled, often includes recycled content in new stainless steel products. Environmental impact slightly higher due to energy-intensive production. |
Metal Fabrication Service Market Insights
As per skyquestt market research report “The global metal fabrication service market was valued at USD 20.94 billion in 2022 and is projected to grow to USD 31.66 billion by 2031, with a compound annual growth rate (CAGR) of 4.7{53ed28d223a4415f45f82b5e3e66625b5ba2d29a1cba4099bda1615b910c8a6d} during the forecast period from 2024 to 2031. This growth is attributed to several factors including the rising adoption of die casting techniques, which are preferred for their efficiency and better dimensional tolerances compared to other methods like sand casting.”
“Regionally, the Asia-Pacific market holds the largest share, approximately 40{53ed28d223a4415f45f82b5e3e66625b5ba2d29a1cba4099bda1615b910c8a6d}, due to significant industrial growth in countries like India, Bangladesh, and Vietnam. These nations are experiencing rapid industrialisation and urbanisation, further boosted by government initiatives such as India’s Make in India campaign. The North American market, particularly the United States, also maintains a strong position in the global market, especially in the welding segment, and is expected to reach a market size of USD 6 billion by 2030.”
The market’s expansion is notably driven by the increasing use of metal fabrication in various industries including automotive, construction, and aerospace. Innovations and technological integrations in fabrication processes are also creating new opportunities for the market.
For detailed insights into the market dynamics, you can access the full report here.
Choosing between Aluminium and stainless steel for fabrication projects involves assessing each metal’s unique properties and how they align with the project’s requirements. Aluminium is favoured for its light weight, corrosion resistance, and excellent conductivity, making it ideal for applications where these attributes are prioritised. On the other hand, stainless steel offers unmatched durability and strength, along with superior resistance to corrosion, which is crucial for more demanding environmental conditions and structural needs. Both metals boast significant recyclability, contributing to environmental sustainability. Ultimately, the decision depends on specific factors such as the intended use, environmental conditions, weight considerations, and cost-effectiveness of the project. By carefully evaluating these aspects, fabricators can make an informed choice that best meets the demands of their specific fabrication challenges.
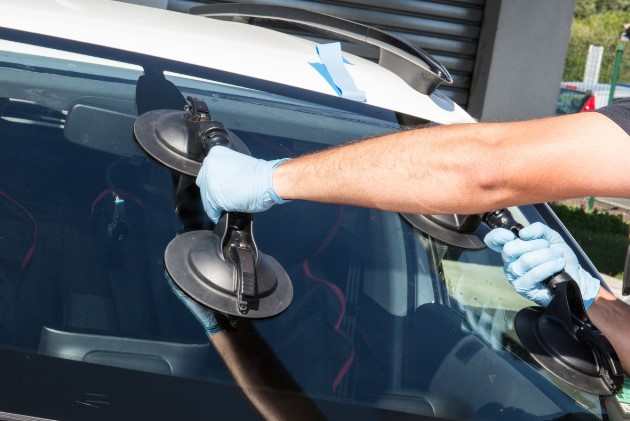
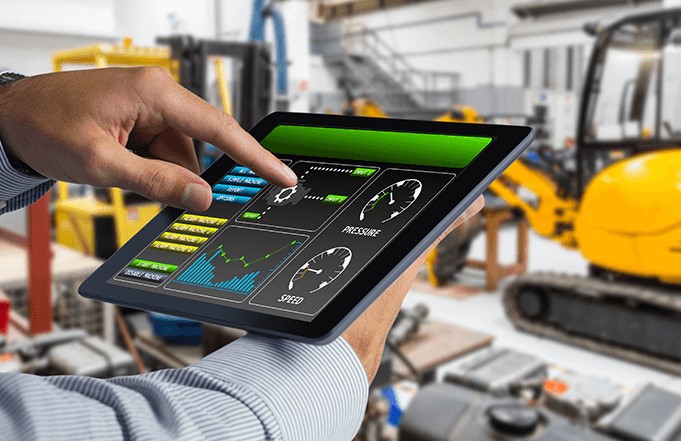