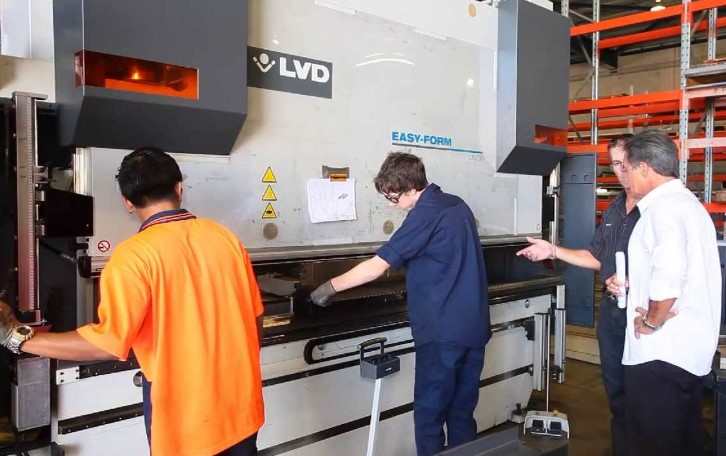
Exploring the World of CNC Press Brakes: Precision in Metal Bending
In the fast-evolving landscape of manufacturing, precision and efficiency are paramount. CNC press brakes have emerged as game-changers in the industry, reshaping the way we bend sheet metal and facilitating the creation of intricate components. These machines offer a level of accuracy that was once only dreamed of, making them indispensable tools for a wide range of applications, from automotive and aerospace to architecture and beyond.
This blog post delves into the world of CNC Press Brake, shedding light on their fundamental aspects, types, brands, safety considerations, and maintenance requirements. Whether you’re an industry professional seeking insights or simply a curious enthusiast eager to learn more, the journey begins here. Let’s explore the precision, versatility, and innovation that CNC press brakes bring to modern manufacturing.
What is a CNC Press Brake?
At the heart of precision metal bending lies the CNC press brake. But what exactly is it, and how does it work? Let’s break it down:
A CNC press brake is a sophisticated machine designed to shape sheet metal with remarkable accuracy. It operates on a simple principle: by clamping the metal sheet between a punch and a die, it creates bends in the material. The magic, however, happens in the precise control it offers.
The “CNC” in CNC press brake stands for “Computer Numerical Control.” This means that these machines are equipped with a computerized system that governs their movements. It’s this high-tech component that allows CNC press brakes to make precise, repeatable bends in sheet metal.
The computer system takes your specifications and translates them into precise movements of the machine’s components. It controls the position and speed of the ram (the part that does the bending) and ensures that the bends are accurate to the tiniest fraction of an inch. This level of precision is something that manual methods simply can’t match.
So, in essence, a CNC press brake is a marvel of modern manufacturing technology, offering unmatched precision and control in bending sheet metal. It’s a vital tool in a variety of industries where accuracy and efficiency are paramount. Now that you know what a CNC press brake is let’s explore how it all works in the next section. For detail CNC press brake you can see it at https://www.thefabricator.com/directory/showroom/metaline-metal-fabrication
The Basics of CNC Press Brakes
Now that we understand what a CNC press brake is, let’s delve deeper into how these remarkable machines work and why they’re at the forefront of precision metal bending.
1. How They Work
At its core, a CNC press brake operates by securely clamping a metal sheet between a punch and a die. The punch is the upper component, while the die is the lower part. The machine’s computer control system takes over from there, orchestrating a series of precise movements to create the desired bend in the metal.
The key here is the ability to control not just the position of the punch and die but also the speed at which they move. This level of control is what distinguishes CNC press brakes from conventional, manual methods. It ensures consistent and repeatable results, which are crucial in modern manufacturing.
2. Precision and Accuracy
One of the most significant advantages of CNC press brakes is the unmatched precision they provide. The computer control system can calculate and adjust the position and speed of the bending components down to the micron. This means that whether you’re bending a thin sheet of aluminum or a thick piece of steel, the result is always exactly as intended.
3. Versatility
CNC press brakes are incredibly versatile, capable of handling a wide range of materials and thicknesses. This versatility makes them indispensable in various industries, from automotive and aerospace to architectural metalwork. Whether you’re creating simple angles or complex, multi-bend components, CNC press brakes can handle the task.
Their adaptability extends to the types of bends they can create, including V-bending, U-bending, and more. This flexibility opens up a world of possibilities for manufacturers looking to meet diverse production needs.
In summary, CNC press brakes are the epitome of precision, offering control, accuracy, and versatility in metal bending. The combination of advanced technology and expert engineering has made these machines a cornerstone of modern manufacturing. Now that we’ve covered the basics, it’s time to explore the different types of CNC press brakes and the advantages they bring.
Types of CNC Press Brakes
CNC press brakes come in several variations, each designed to cater to specific needs and requirements in the world of metal bending. Let’s take a closer look at the various types:
1. Hydraulic CNC Press Brake
Hydraulic CNC press brakes are renowned for their power and flexibility. They rely on hydraulic cylinders to control the movement of the machine’s ram. Here’s what sets them apart:
- Powerful Bending: Hydraulic press brakes are capable of exerting significant force, making them suitable for bending thick and heavy metal sheets.
- Fine Control: The hydraulic system allows for precise control over the bending process, ensuring that even complex bends are achieved accurately.
- Versatility: They can handle a wide range of materials and thicknesses, making them a popular choice in industries where versatility is key.
2. Servo-Electric CNC Press Brake
Servo-electric CNC press brakes represent a leap in precision and energy efficiency. They use a combination of electric motors and ball screws to control the bending process:
- Unmatched Precision: Servo-electric press brakes offer exceptional control, making them ideal for jobs that demand the utmost precision.
- Energy Efficiency: They are more energy-efficient than hydraulic counterparts, helping to reduce operational costs.
- Quiet Operation: Servo-electric press brakes are known for their quiet and clean operation, making them suitable for various work environments.
3. Manual CNC Press Brake
While less common than hydraulic and servo-electric press brakes, manual CNC press brakes offer a unique advantage: operator control. Here’s what you need to know:
- Hands-On Bending: Manual press brakes provide operators with a high level of control over the bending process. This makes them ideal for custom and small-scale projects where fine-tuning is crucial.
- Cost-Effective: They are often more budget-friendly than their automated counterparts, making them an attractive option for smaller businesses.
- Customizability: Manual CNC press brakes allow for adjustments and experimentation, making them well-suited for niche or specialized applications.
In conclusion, the choice of CNC press brake depends on the specific needs of a project or operation. Hydraulic press brakes offer power and versatility, servo-electric press brakes provide precision and energy efficiency, while manual press brakes grant operators greater control. Selecting the right type is crucial in achieving the desired results for your metal bending projects. Now, let’s explore the prominent brands that manufacture these CNC press brakes and what sets them apart.
CNC Press Brake Brands
When it comes to CNC press brakes, the brand you choose can significantly impact the quality, performance, and features of your machine. Let’s explore some of the prominent CNC press brake brands and what sets them apart:
1. Amada CNC Press Brake
- Reputation for Quality: Amada is renowned for producing high-quality CNC press brakes known for their precision and reliability.
- Innovative Technology: The brand is synonymous with cutting-edge technology, incorporating advanced features that enhance the bending process.
- Extensive Product Range: Amada offers a wide range of press brakes, from compact models for small shops to large, automated machines for industrial-scale production.
2. Trumpf CNC Press Brake
- Leadership in Bending Technology: Trumpf is a global leader in sheet metal bending technology, and their CNC press brakes reflect this expertise.
- Integration with Software Solutions: Trumpf press brakes often integrate seamlessly with software solutions for precise control and efficient programming.
- Durability and Precision: The brand is known for producing durable machines that provide precise and consistent bending results.
3. Bystronic CNC Press Brake
- Shaping the Future: Bystronic is at the forefront of shaping the future of metal fabrication with its innovative CNC press brakes.
- Smart Manufacturing Solutions: Bystronic’s machines are often part of a broader smart manufacturing ecosystem, incorporating automation and software solutions for increased productivity.
- Customization Options: The brand offers customization options, allowing customers to tailor their CNC press brakes to specific requirements.
4. Haco CNC Press Brake
- European Quality: Haco, a European brand, is recognized for producing high-quality CNC press brakes known for their robust build and precision.
- Wide Range of Models: Haco offers a wide range of press brake models, from small hydraulic machines to large, synchronized systems.
- User-Friendly Control: Their press brakes are often equipped with user-friendly controls for ease of operation.
5. Accurpress CNC Press Brake
- North American Precision: Accurpress, a North American brand, is respected for producing precision CNC press brakes tailored to the needs of the North American market.
- Advanced Control Systems: Accurpress press brakes often come equipped with advanced control systems for efficient programming and operation.
- Customization and Support: The brand focuses on providing customization options and exceptional customer support to meet specific customer needs.
Choosing the right brand for your CNC press brake is a crucial decision, as it can impact your business’s productivity and efficiency. Each of these brands offers unique advantages, from innovative technology to exceptional precision and durability. Consider your specific needs and the reputation of the brand when making your selection.
Safety and Maintenance
Operating CNC press brakes efficiently and safely is paramount to ensure the well-being of operators and the longevity of the machines. In this section, we’ll explore the essential aspects of safety and maintenance in the context of CNC press brakes:
1. Safety Measures in CNC Press Brakes
Safety should always be the top priority when working with CNC press brakes. Here are some key safety measures to consider:
- Guarding Systems: CNC press brakes are equipped with guarding systems that protect operators from the moving parts of the machine. It’s crucial to ensure these guards are always in place and functioning correctly.
- Safety Training: Operators should undergo comprehensive safety training to understand the risks associated with CNC press brakes and how to operate them safely. This includes proper handling of materials and understanding emergency procedures.
- Risk Assessment: Regular risk assessments should be conducted to identify and mitigate potential hazards. This includes evaluating factors such as tooling, materials, and the workspace environment.
2. CNC Press Brake Guarding
Guarding systems are a critical component of safety in CNC press brake operation. They include:
- Light Curtains: Light curtains are sensors that create an invisible barrier. If this barrier is broken, the machine stops immediately, preventing accidents.
- Physical Barriers: Physical guarding, such as interlocked safety doors, provides a physical barrier between the operator and moving parts of the press brake.
- Safety Mats: Safety mats are pressure-sensitive devices that, when stepped on, trigger an emergency stop.
3. Safety Training for CNC Press Brake
Ensuring that operators are well-trained in safety protocols is vital for preventing accidents. Safety training should cover:
- Machine Familiarization: Operators should be familiar with the CNC press brake’s components, controls, and operating procedures.
- Material Handling: Proper techniques for handling and positioning materials on the machine should be taught to reduce the risk of injury.
- Emergency Procedures: Operators must know how to respond to emergencies, including how to shut down the machine in case of a malfunction or if someone is at risk.
4. Preventive Maintenance
Regular maintenance is essential to keep CNC press brakes in optimal working condition. Key maintenance activities include:
- Lubrication: Adequate lubrication of moving parts is crucial to reduce friction and prevent wear and tear. Follow the manufacturer’s guidelines for lubrication schedules.
- Tool Inspection: Regularly inspect and maintain the machine’s tooling to ensure it is sharp and in good condition. Dull or damaged tools can result in suboptimal bends and can stress the machine.
- Electrical Systems: Periodic inspection of the electrical systems is important to prevent issues related to wiring, connections, and control systems.
- Calibration: Calibrating the CNC press brake’s control system ensures that it continues to produce accurate bends. Regular calibration checks should be part of your maintenance routine.
Safety and maintenance go hand in hand in ensuring the safe and efficient operation of CNC press brakes. Regular inspections, safety measures, and ongoing training help prevent accidents and maintain the machine’s performance. Adhering to these principles is essential for a productive and secure working environment.
Conclusion
In the realm of precision metal bending, CNC press brakes stand as both a technological marvel and an essential tool for modern manufacturing. The journey through this exploration of CNC press brakes has revealed their significance and versatility in shaping the future of metal fabrication.
In this comprehensive guide, we’ve covered the following key aspects:
- Understanding CNC Press Brakes: We began by unraveling the concept of CNC press brakes, delving into how these machines use computer numerical control to achieve unparalleled accuracy in bending sheet metal.
- The Basics of CNC Press Brakes: Next, we explored the fundamental workings of CNC press brakes, highlighting their precision and versatility. From complex geometries to heavy-duty applications, these machines have revolutionized metal bending.
- Types of CNC Press Brakes: We then ventured into the world of hydraulic, servo-electric, and manual CNC press brakes, each with its unique advantages. Your choice of press brake type depends on the specific requirements of your projects.
- CNC Press Brake Brands: Prominent CNC press brake manufacturers, including Amada, Trumpf, Bystronic, Haco, and Accurpress, were introduced. Each brand offers distinct features and strengths, enabling you to select the right fit for your needs.
- Safety and Maintenance: Ensuring the safety of operators and the longevity of CNC press brakes is paramount. We discussed the importance of safety measures, guarding systems, safety training, and preventive maintenance.
As you navigate the world of CNC press brakes, remember that these machines empower you to achieve the precision, consistency, and efficiency that modern manufacturing demands. Whether you’re a seasoned professional seeking the latest innovations or a newcomer to the industry, CNC press brakes continue to shape the landscape of metal fabrication.
With their robust features and versatile capabilities, CNC press brakes have become indispensable tools in industries ranging from automotive and aerospace to architecture and beyond. As technology evolves and manufacturing techniques advance, CNC press brakes will undoubtedly remain at the forefront, continually pushing the boundaries of what’s achievable in metal bending.
We hope this guide has provided valuable insights into CNC press brakes and their role in the world of manufacturing. If you have further questions, seek advice, or are ready to embark on your journey with these remarkable machines, don’t hesitate to explore the possibilities that CNC press brakes offer. This article is brought to you by Metaline, a Canadian metal fabrication factory, that recently has started to offer engineering assistance on top of their labor and production services.
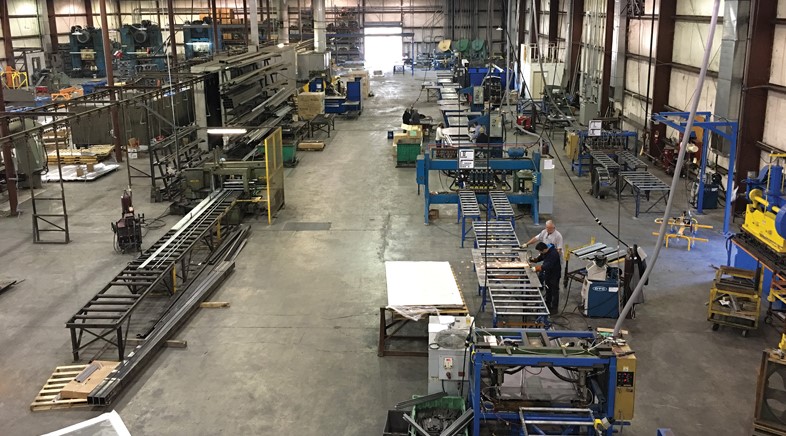
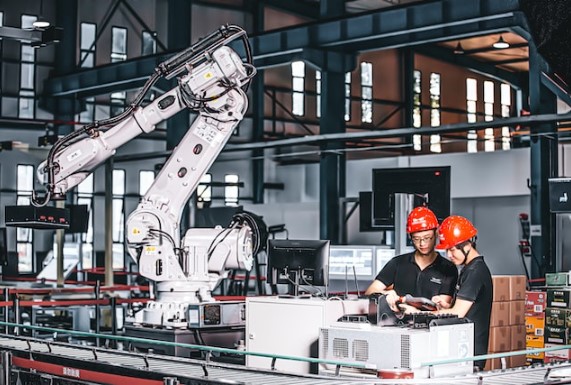