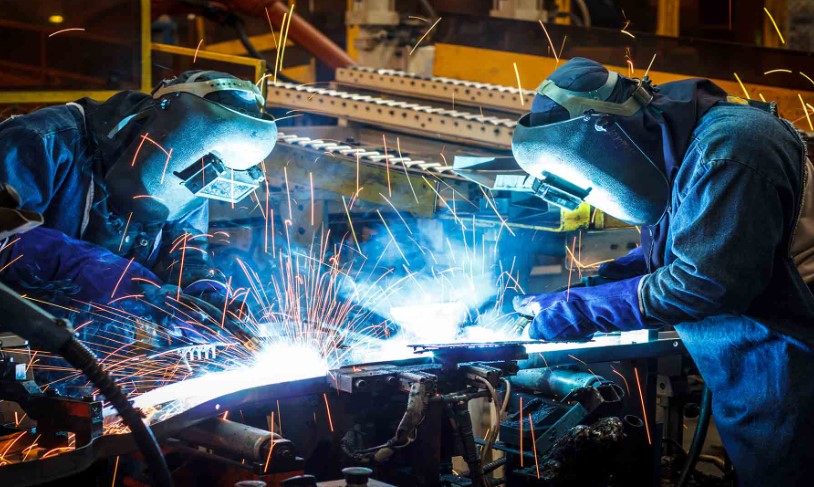
Manufacturing Engineering: Empowering Innovation and Efficiency
Manufacturing engineering plays a pivotal role in transforming raw materials into finished products efficiently and economically. With its blend of technical knowledge, creativity, and problem-solving skills, this field drives innovation and shapes the future of various industries. In this article, we will explore the intricacies of manufacturing engineering, its importance, key concepts, processes, and the exciting opportunities it offers. Whether you are a student considering a career in manufacturing engineering or an industry professional seeking to enhance your knowledge, this article will provide valuable insights into this dynamic field.
1. Introduction
In today’s rapidly evolving world, manufacturing engineering is at the forefront of innovation and productivity. It encompasses a wide range of disciplines, including mechanical engineering, industrial engineering, materials science, and computer-aided design. By applying scientific principles and advanced technologies, manufacturing engineers optimize production processes, improve product quality, reduce costs, and ensure sustainability.
2. What is Manufacturing Engineering?
Manufacturing engineering can be defined as the branch of engineering that focuses on the design, development, implementation, and improvement of manufacturing processes and systems. It involves the integration of machines, tools, materials, and human resources to create efficient and cost-effective production methods. Manufacturing engineers work collaboratively with design engineers, supply chain professionals, and quality assurance teams to ensure seamless product realization from concept to delivery.
3. Importance of Manufacturing Engineering
Manufacturing engineering plays a vital role in the success of businesses across various sectors. Here are some key reasons why it is important:
Enhancing Efficiency and Productivity
In the highly competitive global market, companies strive to maximize their productivity and efficiency. Manufacturing engineers optimize production workflows, eliminate bottlenecks, and streamline operations to ensure timely delivery of high-quality products. Their expertise in process optimization, automation, and lean manufacturing methodologies enables businesses to stay ahead of the competition.
Driving Innovation and New Product Development
Manufacturing engineering is the breeding ground for innovation. By leveraging advanced technologies such as additive manufacturing, robotics, and digital simulation, engineers can push the boundaries of what is possible. They collaborate with R&D teams to develop new products, improve existing ones, and explore novel manufacturing techniques that open doors to exciting opportunities.
Ensuring Quality and Reliability
Manufacturing engineers are responsible for maintaining stringent quality standards throughout the production process. They develop quality control systems, conduct inspections, and implement corrective actions to minimize defects and ensure product reliability. By adhering to industry standards and employing statistical analysis techniques, they contribute to customer satisfaction and brand reputation.
4. Role of Manufacturing Engineers
Manufacturing engineers assume multifaceted roles within organizations. Some of their key responsibilities include:
Process Design and Optimization
Manufacturing engineers design production processes, considering factors such as material selection, equipment capabilities, and cost efficiency. They analyze the requirements, identify potential bottlenecks, and devise strategies to optimize the manufacturing workflow.
Equipment Selection and Implementation
Manufacturing engineers evaluate and select the appropriate machinery, tools, and equipment for specific manufacturing processes. They ensure that the chosen equipment aligns with the production requirements, quality standards, and budget constraints. Additionally, they oversee the installation, testing, and maintenance of the equipment to ensure smooth operations.
Automation and Robotics Integration
Automation and robotics have revolutionized the manufacturing industry. Manufacturing engineers play a crucial role in implementing automated systems and robotic solutions. They program robots, develop production lines, and integrate advanced technologies to enhance efficiency, precision, and productivity.
Supply Chain Management
Manufacturing engineers collaborate with supply chain professionals to ensure the seamless flow of materials and components. They work on optimizing inventory levels, managing suppliers, and implementing effective logistics strategies. By streamlining the supply chain, they minimize delays, reduce costs, and enhance overall operational efficiency.
Continuous Improvement and Lean Practices
Continuous improvement is the cornerstone of manufacturing engineering. Engineers actively seek opportunities to enhance processes, eliminate waste, and improve overall performance. They employ lean manufacturing principles, such as value stream mapping, 5S, and Kaizen, to drive continuous improvement initiatives and maximize productivity.
5. Key Concepts in Manufacturing Engineering
To understand manufacturing engineering comprehensively, it is essential to grasp the key concepts that form its foundation. Here are some important concepts in the field:
CAD/CAM
Computer-Aided Design (CAD) and Computer-Aided Manufacturing (CAM) are essential tools in manufacturing engineering. CAD enables engineers to create detailed 2D or 3D models of products and components, while CAM facilitates the generation of machine instructions to manufacture those designs accurately.
Materials Science
A solid understanding of materials science is crucial for manufacturing engineers. They study the properties, behavior, and characteristics of materials to select the most suitable ones for specific applications. Materials science encompasses areas such as metallurgy, polymers, composites, and ceramics.
Statistical Process Control (SPC)
SPC is a statistical technique used to monitor and control manufacturing processes. It involves collecting and analyzing data to identify variations and deviations from the desired specifications. By applying SPC techniques, manufacturing engineers can ensure consistent product quality and make data-driven decisions for process improvement.
Six Sigma
Six Sigma is a methodology that focuses on reducing defects and improving process efficiency. Manufacturing engineers employ Six Sigma tools and techniques, such as DMAIC (Define, Measure, Analyze, Improve, Control), to identify root causes of variation, implement process improvements, and achieve higher levels of quality and customer satisfaction.
6. Manufacturing Processes and Techniques
Manufacturing engineering encompasses a wide range of processes and techniques tailored to different industries and product requirements. Here are some common manufacturing processes:
Machining
Machining involves the removal of material from a workpiece to achieve the desired shape and size. Processes such as milling, turning, drilling, and grinding fall under machining. Computer Numerical Control (CNC) machines play a crucial role in automating machining operations.
Casting
Casting is a process in which molten metal or other materials are poured into a mold and allowed to solidify. It is widely used for creating complex shapes and components. Casting methods include sand casting, investment casting, die casting, and more.
Forming
Forming processes involve the shaping of materials using mechanical forces. Examples include forging, stamping, bending, and extrusion. These processes are utilized to create components with specific geometries and properties.
Additive Manufacturing
Additive manufacturing, also known as 3D printing, is a transformative technology in manufacturing engineering. It involves building objects layer by layer using various materials such as plastics, metals, or ceramics. Additive manufacturing enables the production of complex designs, customization, and rapid prototyping.
Welding and Joining
Welding and joining processes are used to fuse multiple parts together. Techniques such as arc welding, laser welding, and brazing are employed to create strong and durable connections. Welding plays a vital role in industries such as automotive, aerospace, and construction.
Assembly and Integration
Assembly is the process of joining individual components to create a finished product. It involves the coordination of various sub-assemblies, fasteners, and adhesives. Manufacturing engineers ensure smooth assembly operations, efficient workflow, and proper quality control during the assembly process.
7. Automation and Robotics in Manufacturing Engineering
Automation and robotics have revolutionized the manufacturing industry, enhancing productivity, precision, and efficiency. Manufacturing engineers leverage these technologies to streamline processes and achieve higher levels of performance. Here are some key aspects of automation and robotics in manufacturing engineering:
Industrial Robotics
Industrial robots are programmable machines that automate repetitive tasks, such as material handling, assembly, and welding. Manufacturing engineers design robotic workcells, program robots, and integrate them into the production line. Robots not only improve productivity but also enhance workplace safety by handling hazardous operations.
Automated Guided Vehicles (AGVs)
AGVs are autonomous vehicles used for material transportation within a manufacturing facility. Manufacturing engineers deploy AGVs to automate material flow, optimize logistics, and reduce manual labor. AGVs navigate using sensors, cameras, or magnetic strips and can transport materials efficiently and precisely.
Internet of Things (IoT)
The integration of IoT devices in manufacturing has enabled the concept of the “smart factory.” Manufacturing engineers utilize IoT sensors, connectivity, and data analytics to monitor machines, collect real-time data, and optimize production processes. IoT enables predictive maintenance, remote monitoring, and data-driven decision-making.
Collaborative Robotics
Collaborative robots, or cobots, are designed to work alongside humans in a shared workspace. Manufacturing engineers implement cobots to assist workers in tasks requiring precision, dexterity, or ergonomics. Cobots enhance productivity, reduce physical strain on workers, and facilitate human-robot collaboration.
8. Quality Control and Assurance in Manufacturing
Ensuring product quality and reliability is of utmost importance in manufacturing engineering. Manufacturing engineers implement robust quality control and assurance measures throughout the production process. Here are some key aspects of quality control in manufacturing:
Statistical Quality Control
Statistical techniques are used to monitor and control manufacturing processes. Manufacturing engineers employ methods such as control charts, hypothesis testing, and process capability analysis to ensure that the manufacturing process is within acceptable limits and meets the required quality standards.
Quality Management Systems (QMS)
Quality management systems provide a framework for managing and improving quality within an organization. Manufacturing engineers develop and implement QMS, such as ISO 9001, to establish standardized processes, document procedures, and monitor quality performance. QMS helps ensure consistency and customer satisfaction.
Inspection and Testing
Inspection and testing are integral parts of quality control. Manufacturing engineers define inspection criteria, conduct visual inspections, and employ non-destructive testing methods to identify defects, measure product dimensions, and verify compliance with specifications. Inspection equipment and techniques vary depending on the product and industry.
Failure Analysis and Root Cause Analysis
In the event of product failures or quality issues, manufacturing engineers conduct failure analysis to identify the root causes. They investigate the underlying factors contributing to failures and implement corrective actions to prevent recurrence. Failure analysis helps improve product reliability and identify areas for process improvement.
Supplier Quality Management
Manufacturing engineers collaborate with suppliers to ensure the quality of incoming materials and components. They establish quality requirements, conduct supplier audits, and implement supplier quality management programs. Effective supplier quality management contributes to consistent product quality and reduces the risk of defects.
9. Cost Optimization in Manufacturing Engineering
Cost optimization is a critical aspect of manufacturing engineering, as it directly impacts profitability and competitiveness. Manufacturing engineers employ various strategies to optimize costs throughout the production process. Here are key considerations for cost optimization:
Value Engineering
Value engineering focuses on improving the value of products or processes while reducing costs. Manufacturing engineers analyze product functionalities, material choices, and manufacturing methods to identify opportunities for cost savings without compromising quality or performance. Value engineering enhances efficiency and maximizes the return on investment.
Lean Manufacturing
Lean manufacturing aims to eliminate waste and improve efficiency in production processes. Manufacturing engineers implement lean principles, such as just-in-time manufacturing, 5S methodology, and continuous improvement, to streamline operations, reduce inventory, minimize defects, and optimize resource utilization. Lean manufacturing enables cost savings and enhances overall productivity.
Supply Chain Optimization
Manufacturing engineers collaborate with supply chain professionals to optimize the supply chain and reduce costs. They analyze the supply chain network, identify areas for improvement, and implement strategies to minimize transportation costs, streamline inventory management, and enhance overall supply chain efficiency. Supply chain optimization contributes to cost reduction and improved responsiveness.
Process Optimization
Manufacturing engineers continually analyze and optimize manufacturing processes to improve efficiency and reduce costs. They identify process bottlenecks, eliminate non-value-added activities, and implement process improvements. By optimizing processes, manufacturing engineers reduce cycle times, increase productivity, and minimize waste, leading to cost savings.
10. Environmental Sustainability in Manufacturing
In today’s era of sustainability, manufacturing engineering plays a crucial role in minimizing the environmental impact of production processes. Manufacturing engineers incorporate sustainable practices to reduce resource consumption, waste generation, and carbon footprint. Here are key considerations for environmental sustainability:
Sustainable Materials and Design
Manufacturing engineers emphasize the use of sustainable materials and eco-friendly design principles. They select materials with low environmental impact, promote recycling and reuse, and adopt design strategies that minimize material waste. Sustainable materials and design contribute to reducing the overall environmental footprint of products.
Energy Efficiency
Manufacturing engineers implement energy-efficient technologies and practices to minimize energy consumption in manufacturing processes. They identify energy-intensive operations, optimize equipment and machinery for energy efficiency, and explore renewable energy sources. Energy-efficient manufacturing reduces greenhouse gas emissions and lowers operational costs.
Waste Reduction and Recycling
Manufacturing engineers focus on waste reduction and recycling initiatives. They implement waste management systems, encourage recycling programs, and explore opportunities for waste-to-energy conversion. By reducing waste sent to landfills and promoting recycling, manufacturing engineering contributes to a circular economy and sustainable resource utilization.
Life Cycle Assessment (LCA)
Manufacturing engineers perform life cycle assessments to evaluate the environmental impact of products throughout their entire life cycle. They assess factors such as raw material extraction, production processes, product use, and end-of-life disposal. LCA helps identify areas for improvement, guide sustainable decision-making, and optimize product designs.
11. Future Trends in Manufacturing Engineering
The field of manufacturing engineering is continuously evolving, driven by technological advancements and changing industry needs. Here are some future trends that manufacturing engineers should keep an eye on:
Industry 4.0 and Digitalization
Industry 4.0, also known as the Fourth Industrial Revolution, is characterized by the integration of digital technologies into manufacturing processes. Manufacturing engineers will play a crucial role in implementing technologies such as artificial intelligence, big data analytics, cloud computing, and the Internet of Things (IoT). These technologies will enable real-time monitoring, predictive maintenance, and data-driven decision-making, leading to improved efficiency and productivity.
Advanced Robotics and Cobots
Advancements in robotics will continue to shape the manufacturing landscape. Manufacturing engineers will work with advanced robots that possess increased dexterity, adaptability, and autonomy. Collaborative robots (cobots) will become more prevalent, working alongside humans in a seamless and safe manner. These advancements will enhance productivity, flexibility, and worker safety.
Additive Manufacturing Innovations
Additive manufacturing, or 3D printing, will witness further innovations and applications. Manufacturing engineers will explore new materials, improved printing techniques, and larger-scale printing capabilities. The ability to manufacture complex geometries, customized products, and on-demand spare parts will revolutionize the manufacturing industry.
Sustainable and Green Manufacturing
Environmental sustainability will continue to be a major focus in manufacturing engineering. Manufacturing engineers will drive the adoption of sustainable practices, renewable energy sources, and eco-friendly materials. The integration of circular economy principles and the reduction of carbon emissions will be paramount in achieving sustainable and green manufacturing.
Human-Machine Collaboration
The future of manufacturing will involve closer collaboration between humans and machines. Manufacturing engineers will design work environments that facilitate seamless interaction and communication between humans and robots. They will focus on enhancing ergonomics, safety, and skill development to create a harmonious and efficient human-machine collaboration.
Conclusion
Manufacturing engineering is a dynamic and vital field that encompasses a wide range of processes, technologies, and strategies to optimize production. Manufacturing engineers play a crucial role in designing, optimizing, and managing manufacturing systems while ensuring product quality, cost efficiency, and environmental sustainability. With the rapid advancements in technology, the future of manufacturing engineering holds exciting prospects, including digitalization, automation, and sustainable practices. By staying abreast of emerging trends and embracing innovative solutions, manufacturing engineers will continue to drive the progress and evolution of the manufacturing industry.
FAQs (Frequently Asked Questions)
Q1: What is the role of a manufacturing engineer?
A1: A manufacturing engineer is responsible for designing, optimizing, and managing manufacturing systems and processes. They focus on improving efficiency, productivity, and product quality while considering cost and sustainability factors.
Q2: What skills are important for a manufacturing engineer?
A2: Important skills for a manufacturing engineer include knowledge of manufacturing processes, proficiency in CAD/CAM software, problem-solving abilities, strong analytical skills, and good communication and teamwork skills.
Q3: How does automation impact manufacturing engineering?
A3: Automation enhances manufacturing efficiency, productivity, and precision. It reduces human error, speeds up processes, and enables the integration of advanced technologies. Manufacturing engineers play a key role in implementing automation solutions and optimizing automated systems.
Q4: How does manufacturing engineering contribute to sustainability?
A4: Manufacturing engineering contributes to sustainability by implementing sustainable practices, reducing waste and energy consumption, promoting recycling and reuse, and adopting eco-friendly materials and technologies. Manufacturing engineers drive the adoption of environmentally responsible manufacturing processes.
Partner Site : Business Tips , Health News, Future Technology, Home Decorating, Travel Tips, Classic Car, Online Education, Business Law, Women Fashion, Beauty Salon
